Ensuring an electrically safe work condition is crucial for workplace safety. Electrical hazards can cause severe injuries or even fatalities.
Creating a safe work environment involves understanding and mitigating electrical risks. Workers need proper training and protective measures to stay safe. This blog will explore the essential steps and practices to maintain electrical safety at work. From identifying potential hazards to implementing safety protocols, we will cover everything you need to know.
Whether you’re an employer or an employee, understanding these safety measures is vital. Safety should always be a priority, and with the right knowledge, it can be achieved. Let’s dive into the key elements of establishing an electrically safe work condition and protect everyone in the workplace.
Introduction To Electrical Safety
Electrical safety is vital for anyone working with or around electrical equipment. Faulty wiring, exposed cables, and improper handling can lead to serious injuries or even death. Creating a safe work environment helps protect employees and maintain productivity. This section will cover the importance of electrical safety and common electrical hazards you might encounter.
Importance Of Electrical Safety
Understanding the importance of electrical safety can prevent accidents and save lives. Electrical hazards can cause shocks, burns, and fires. These hazards can have severe consequences for workers and businesses alike.
Employers must train their staff about electrical safety measures. Proper training ensures that employees know how to handle electrical equipment safely. It also teaches them to recognize and report electrical hazards.
Compliance with regulations is also a key aspect of electrical safety. Adhering to standards set by organizations like OSHA can prevent legal issues and fines. It also promotes a culture of safety within the workplace.
Common Electrical Hazards
Electrical hazards are present in many forms. Recognizing these hazards is the first step to preventing accidents.
- Exposed Wires: These can cause shocks and burns. Always ensure wires are properly insulated.
- Overloaded Circuits: Overloading can lead to overheating and fires. Avoid plugging too many devices into a single outlet.
- Wet Conditions: Water and electricity are a deadly combination. Keep electrical equipment away from water sources.
- Faulty Equipment: Regularly inspect and maintain electrical tools and machinery. Replace faulty equipment immediately.
Understanding these common hazards can help you take preventive measures. Always stay vigilant and prioritize safety in your workplace.

Credit: e-hazard.com
Regulatory Standards
Regulatory standards are crucial for ensuring electrically safe work conditions. They provide guidelines and protocols to minimize electrical hazards. Understanding these standards helps create a safer work environment. Two main regulatory bodies set these standards: OSHA and NFPA.
Osha Guidelines
The Occupational Safety and Health Administration (OSHA) sets strict guidelines for electrical safety. These guidelines aim to protect workers from electrical hazards. OSHA standards cover various aspects, from safe work practices to proper equipment usage. They require employers to train workers on electrical safety. OSHA also mandates regular inspections and maintenance of electrical systems.
Nfpa 70e Standards
The National Fire Protection Association (NFPA) developed the NFPA 70E standards. These standards focus on electrical safety in the workplace. They provide detailed instructions on risk assessment and control methods. NFPA 70E covers personal protective equipment (PPE) requirements. It also includes guidelines for safe work practices and procedures.
NFPA 70E and OSHA work together to enhance electrical safety. Following these standards reduces the risk of electrical accidents. Ensure your workplace adheres to both OSHA and NFPA 70E standards for maximum safety.
Risk Assessment
Risk assessment is crucial in creating an electrically safe work condition. It helps identify potential hazards and evaluate the risks. This process ensures the safety of workers and prevents electrical accidents. Let’s dive into the key steps of risk assessment.
Identifying Electrical Hazards
Start by spotting the sources of electrical danger. Check for exposed wires, faulty equipment, and wet areas near electrical outlets. Look for signs of wear and tear on cords and plugs. Note any overloaded circuits or improper grounding. Identifying these hazards is the first step in preventing accidents.
Evaluating Risk Levels
After identifying hazards, evaluate the risk level of each. Consider the likelihood of an incident happening. Assess the potential impact on workers. High-risk areas need immediate attention. Use a risk matrix to categorize risks. This helps in prioritizing safety measures. Ensure all team members understand the risks. Their awareness can save lives.
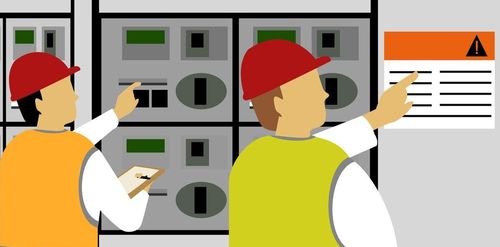
Credit: eltra-trade.com
Safe Work Practices
Creating an electrically safe work condition is essential in any workplace. Safe work practices help minimize risks and ensure safety. By following these practices, workers can protect themselves and their coworkers from electrical hazards. Two key components of safe work practices are Lockout/Tagout procedures and the use of personal protective equipment.
Lockout/tagout Procedures
Lockout/Tagout procedures prevent electrical accidents. They involve isolating energy sources and locking them out. This ensures that machines or equipment cannot be turned on accidentally. Clear tags warn others that the equipment should not be used. Following these steps can save lives. Always verify that the equipment is de-energized before starting work. Proper training is vital for all employees involved.
Use Of Personal Protective Equipment
Personal protective equipment (PPE) is crucial for electrical safety. PPE includes items like gloves, helmets, and safety glasses. These items protect workers from electrical shocks and burns. Always inspect PPE before use. Ensure it is in good condition. Wear the right PPE for the specific task. Training on the proper use of PPE is essential. This helps workers understand its importance and how to use it correctly.
Training And Education
Ensuring an electrically safe work condition requires proper training and education. Employees must know how to handle electrical equipment safely. This blog post discusses essential training programs and continuous education for electrical safety.
Employee Training Programs
Employee training programs are vital for electrical safety. These programs teach workers about potential hazards. They also provide hands-on experience with safety procedures.
Training programs cover topics like lockout/tagout procedures. They also include personal protective equipment (PPE) usage. Workers learn to identify and avoid electrical hazards. This knowledge helps prevent accidents and injuries.
Continuous Education
Continuous education keeps employees updated on safety standards. Electrical safety guidelines often change. Ongoing learning ensures workers stay informed.
Regular refresher courses are essential. They reinforce safety practices and introduce new techniques. Seminars and workshops provide additional learning opportunities. Employees can share experiences and learn from experts.
Continuous education also involves keeping certifications up to date. Employers should encourage and support this. Well-educated employees create a safer work environment.
Emergency Response
Emergency response is crucial in maintaining an electrically safe work condition. Being prepared can save lives. Knowing the steps to take during an emergency ensures everyone’s safety. This section covers essential aspects of emergency response.
First Aid For Electrical Injuries
Electrical injuries can be severe. Immediate first aid is vital. First, do not touch the victim directly. Turn off the power source if possible. Use a non-conductive object to separate the person from the source. Check for breathing and pulse. If the person is not breathing, start CPR immediately. Call emergency services right away. Cover any burns with a sterile gauze bandage. Keep the victim warm and calm until help arrives.
Emergency Evacuation Plans
Having a clear evacuation plan is essential. Ensure all employees know the plan. Conduct regular drills to practice. Identify all exits and ensure they are accessible. Mark escape routes clearly. Assign roles to employees for guiding others. Use alarms or signals to indicate an emergency. Keep first aid kits and fire extinguishers accessible. Review and update the plan regularly. A well-prepared team can evacuate swiftly and safely.
Maintenance And Inspection
Ensuring an electrically safe work condition requires regular maintenance and inspection of all electrical equipment. This helps to identify potential hazards and prevent accidents. Let’s explore the key aspects of maintenance and inspection.
Regular Equipment Inspections
Conducting regular inspections is crucial for maintaining electrical safety. These inspections involve checking for:
- Signs of wear and tear
- Loose connections
- Damaged insulation
- Corrosion
Use a checklist to ensure all aspects are covered:
Inspection Area | What to Check |
---|---|
Wires and Cables | Look for frays and cracks |
Connectors | Ensure they are tight and corrosion-free |
Insulation | Check for any damage or wear |
Switches | Verify they operate smoothly |
Document findings and address issues promptly. This proactive approach prevents accidents and ensures a safe working environment.
Preventive Maintenance
Preventive maintenance involves regular servicing of equipment to keep it in optimal condition. Key activities include:
- Cleaning components to remove dust and debris
- Lubricating moving parts
- Tightening loose connections
- Replacing worn-out parts
Schedule maintenance activities based on equipment usage and manufacturer recommendations. Use a maintenance log to track work performed:
Date | Equipment | Maintenance Task | Technician |
---|---|---|---|
2023-01-15 | Generator | Oil change | John Doe |
2023-02-20 | Transformer | Insulation check | Jane Smith |
Preventive maintenance reduces downtime and extends equipment life. Most importantly, it ensures a safe working environment by addressing potential issues before they become hazards.
Creating A Safety Culture
Creating a safety culture is vital to maintaining an electrically safe work environment. It involves proactive measures, continuous education, and a shared commitment to safety. This culture ensures that everyone in the workplace understands the importance of safety and takes necessary steps to avoid electrical hazards.
Promoting Safety Awareness
Promoting safety awareness is the first step in creating a safety culture. Regular training sessions are essential. These sessions should cover the basics of electrical safety, proper use of equipment, and emergency procedures.
- Conduct monthly safety meetings.
- Distribute safety manuals and guidelines.
- Use posters and signs to remind workers of safety practices.
Additionally, visual aids and hands-on demonstrations can help reinforce the message. Encourage employees to ask questions and clarify doubts to ensure they fully understand the procedures.
Encouraging Reporting Of Hazards
Encouraging the reporting of hazards is another crucial aspect. Workers should feel comfortable reporting potential dangers without fear of repercussions. This can be achieved by establishing clear reporting procedures and ensuring anonymity if needed.
Here are some steps to encourage reporting:
- Set up an easy-to-use reporting system.
- Ensure reports are reviewed and acted upon promptly.
- Provide feedback to employees on the actions taken.
Steps | Description |
---|---|
1 | Establish reporting procedures |
2 | Review and act on reports |
3 | Provide feedback |
Fostering a culture where safety is prioritized helps prevent accidents. It ensures that all employees are invested in maintaining a safe work environment.
Frequently Asked Questions
What Is An Electrically Safe Work Condition?
An electrically safe work condition is when electrical hazards are eliminated. This ensures a safe environment for workers performing tasks.
Why Is Electrically Safe Work Condition Important?
It prevents electrical accidents and injuries. Ensuring electrically safe work conditions protects workers and promotes a safer workplace.
How To Achieve An Electrically Safe Work Condition?
De-energize electrical equipment before work. Use proper lockout/tagout procedures and verify zero energy state.
What Are The Steps For Lockout/tagout?
Identify energy sources, isolate them, and apply lockout/tagout devices. Verify isolation and ensure zero energy before work starts.
Conclusion
Creating an electrically safe work condition is essential. It protects workers from harm. Safety measures should always be a priority. Regular training ensures everyone knows the risks. Proper tools and equipment make a big difference. Always check for hazards before starting any task.
Clear guidelines help maintain a safe environment. Remember, safety saves lives. By following these steps, workplaces can stay accident-free. Everyone deserves to work in a safe setting. Let’s make electrical safety a daily habit.